Incorporating Parking into Mixed-Use Development with Precast Concrete
06/06/2022
Single-use commercial, residential, and office buildings are becoming the exception rather than the rule, particularly in urban and suburban areas. Instead, mixed-use structures have emerged as a safeguard for owners and developers who want to maximize land value AND respond to customer demands for a sense of community where they work, live, and play.
Mixed-Use Structures combine two or more different zoning occupancies into one development - typically commercial and residential, but other types such as cultural, institutional, or industrial can also be included. One significant advantage of mixed-use structures is the ability to maximize the function of a single lot - whether new or revitalized, in urban centers where the desire for a community atmosphere is expanding and the availability of real estate is shrinking.
Parking is an essential piece of the mixed-use puzzle. When constructing new residential apartments, shops, restaurants, or offices, parking is crucial in combating urban density, and traffic congestion is often a local zoning requirement. Precast Concrete, alone or as part of a hybrid system, provides a superior solution for parking within mixed-use development.
Precast Concrete Parking in Mixed-Use Development
Precast concrete outranks other building materials used for parking structures. The offsite fabrication of precast products in Precast Prestressed Concrete Institute (PCI) certified production facilities leads to higher quality construction, reduced cost, accelerates building schedules, and enables versatile design. Designers can utilize the advantages of precast concrete in mixed-use construction with a few different structure types.
Total Precast Mixed-Use Structures
Precast concrete on its own can be used to create the entirety of a mixed-use structure. Precast exterior walls are integrated with the structural system and can be constructed in long spans, usually up to 60 feet, allowing flexibility in design and increasing usable space between columns.
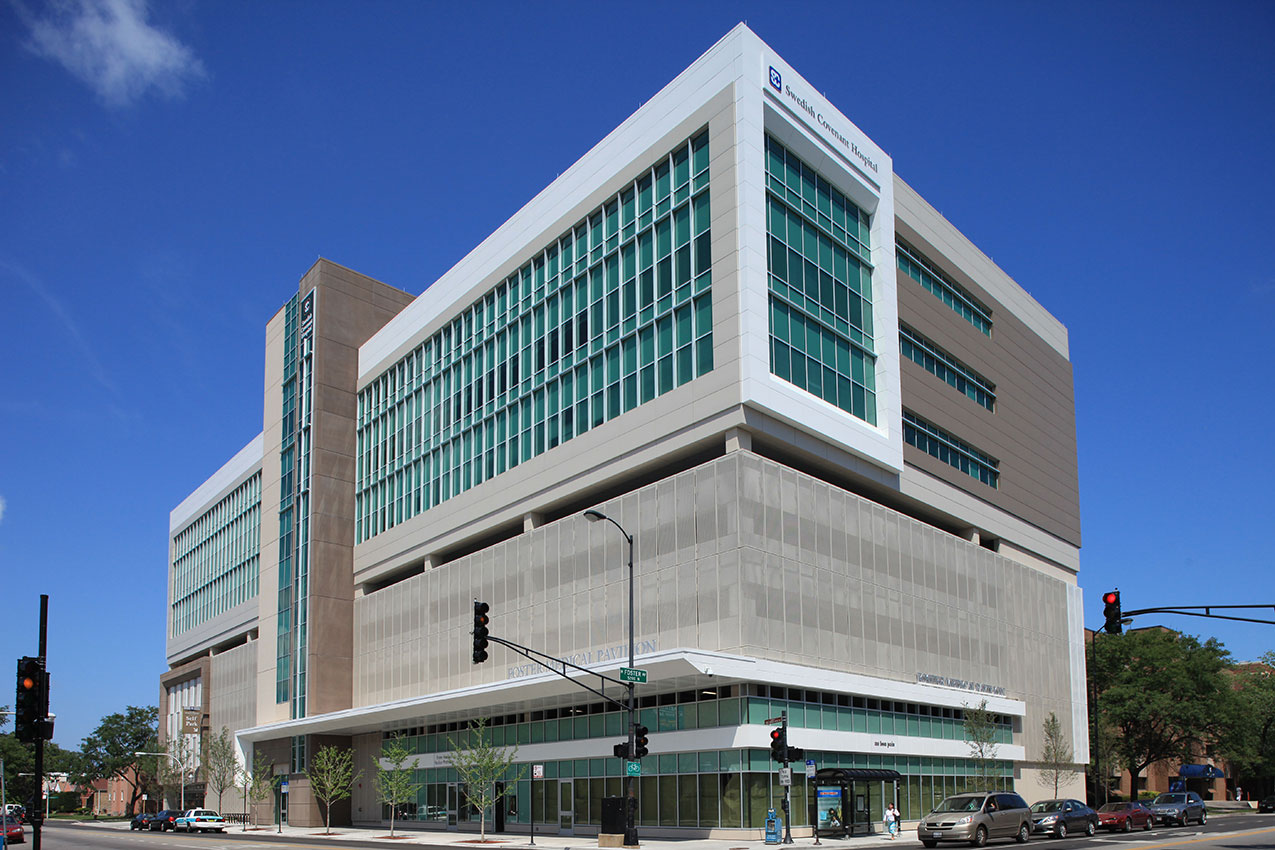
Swedish Covenant Parking and Medical Commons
When using precast concrete as the sole structural component of a building, fabrication can occur concurrently with the site work. Precast concrete reduces the number of required trades, accelerating the project schedule. For Example, at the Swedish Covenant Parking Garage and Medical Commons project in Chicago, IL, building, framing, and parking garage construction was completed in only 7.5 weeks due to the total-precast concrete system. The precast concrete system diminishes vibration and reduces noise transmission, ensuring that the soothing environment created in the surgery center's upper three floors is not disturbed by noise or vibrations from the parking structure.
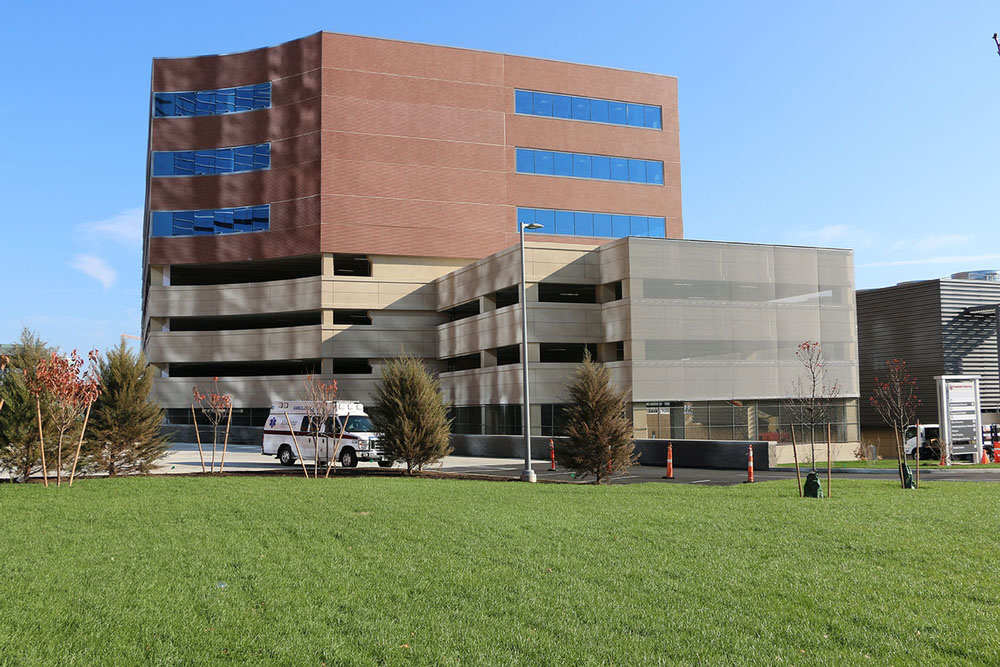
Stamford Integrated Care Pavilion & Medical Office Building
Similarly, the Stamford Integrated Care Pavilion & Medical Office Building project in Stamford, CT, chose precast concrete as the sole structural building element, but not just for time savings - aesthetic value was a driving factor. "The significant advantage that precast concrete provided was that it offered a consistent and uniform structure and appearance throughout the medical parking levels," stated Robert Koenig, Senior Project Manager at Suffolk Construction. Originally designed as two separate buildings, the project contractor recommended combining the office and parking requirements, resulting in an integrated plan that maximized the use of a precast concrete structural framing system.
Hybrid Mixed-Use Structures
Precast concrete can be used alongside other structural components, such as structural steel to create hybrid mixed-use structures. Typically, precast concrete is used at the base of the structure for the parking garage, while structural framing builds out the above retail, office, or residential space.
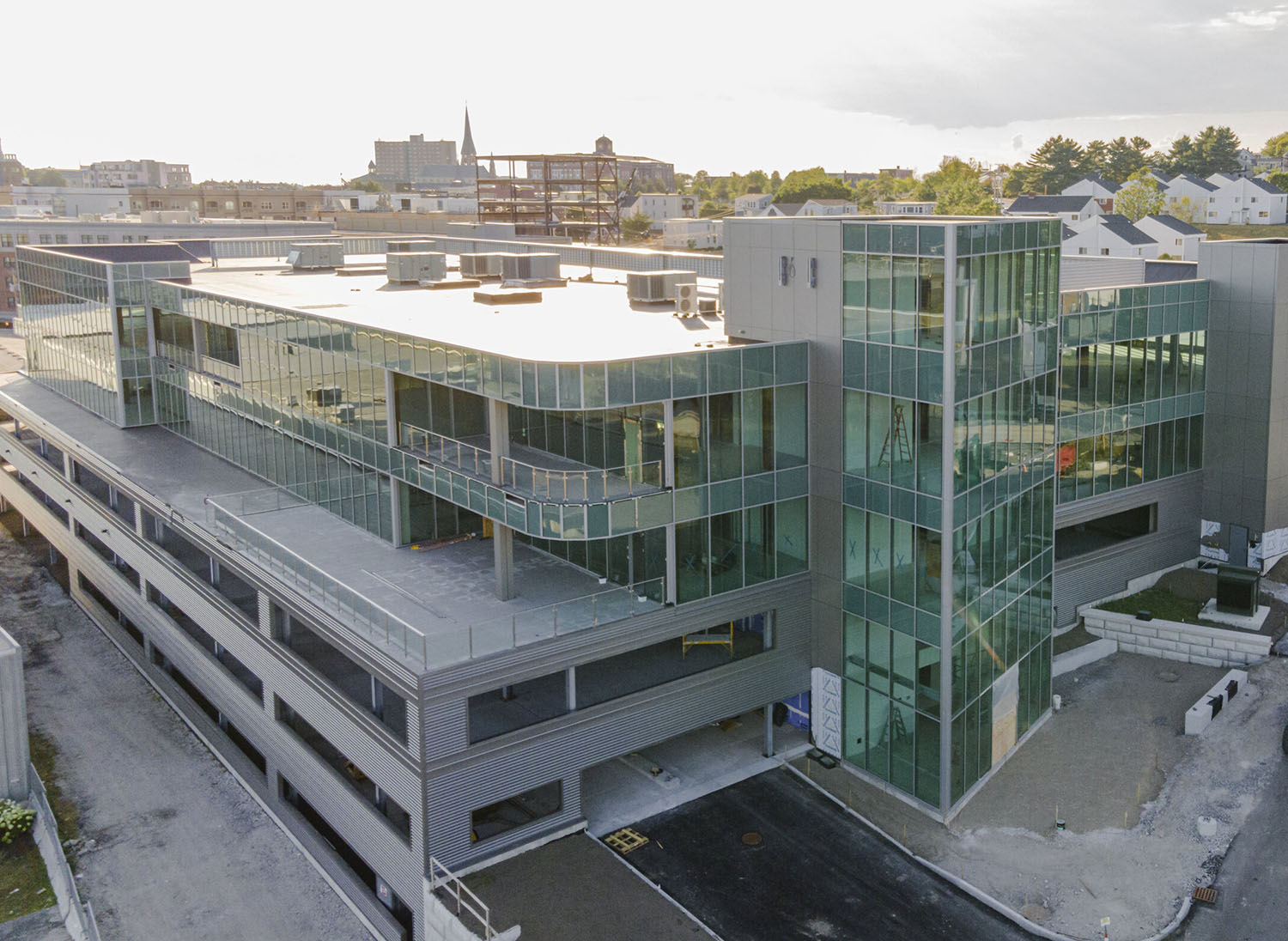
100 Fore Street Mixed-Use Parking
An owner or developer may opt for a hybrid structure to meet specific design criteria. The 100 Fore Street Mixed-Use Parking project in Portland, ME, used a combination of precast concrete floor members and structural steel framing members to construct a 275,000 SF structure complete with 589 parking spaces and 86,000 SF of office and retail space. The structural steel frame allowed glass curtain walls to wrap around the building. At the same time, the precast concrete parking deck enabled lean construction methods, enabling construction within a tight footprint, and accelerating the project schedule.
Parking as a Separate Structure
Mixed-use structures are often thought of as one building with many functions. This type of mixed-use development is known as vertical mixed-use. Another type, horizontal mixed-use development, combines two or more single buildings within a mixed-use zoning parcel. Horizontal mixed-use development is usually a city block containing many separate buildings with integrated uses.
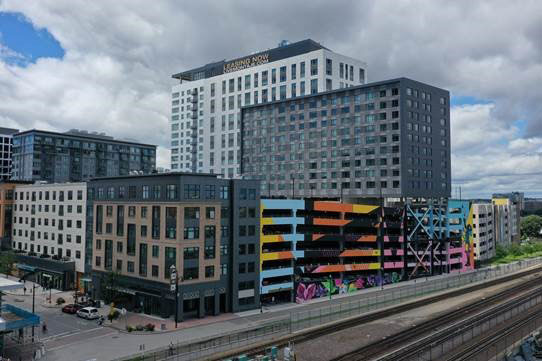
Assembly Row Block 6 Parking Garage
Horizontal mixed-use development enables the option to construct a parking garage as a separate, solo structure. For example, Assembly Row Block 6 Parking Garage in Somerville, MA, created a 7-story parking garage structure to replace a formerly contaminated industrial site. The parking lot is adjoined by residential structures and the city's tallest building.
This 2021 PCI Design Award-winning parking structure used hybrid structural components - steel bracing frames on the exterior, steel columns bearing shared shear walls to support a nearby residential tower, and the rest of precast concrete. Additionally, the entire transit-oriented development project, including Assembly Row Blocks 5A & 6, feature the versatility of precast concrete. An architectural precast exterior and hollow-core floors were utilized in Block 5, the 13-story Alloy Residences & Autograph Collection Hotel, and in Block 6, a 20-story, 273-unit apartment building.
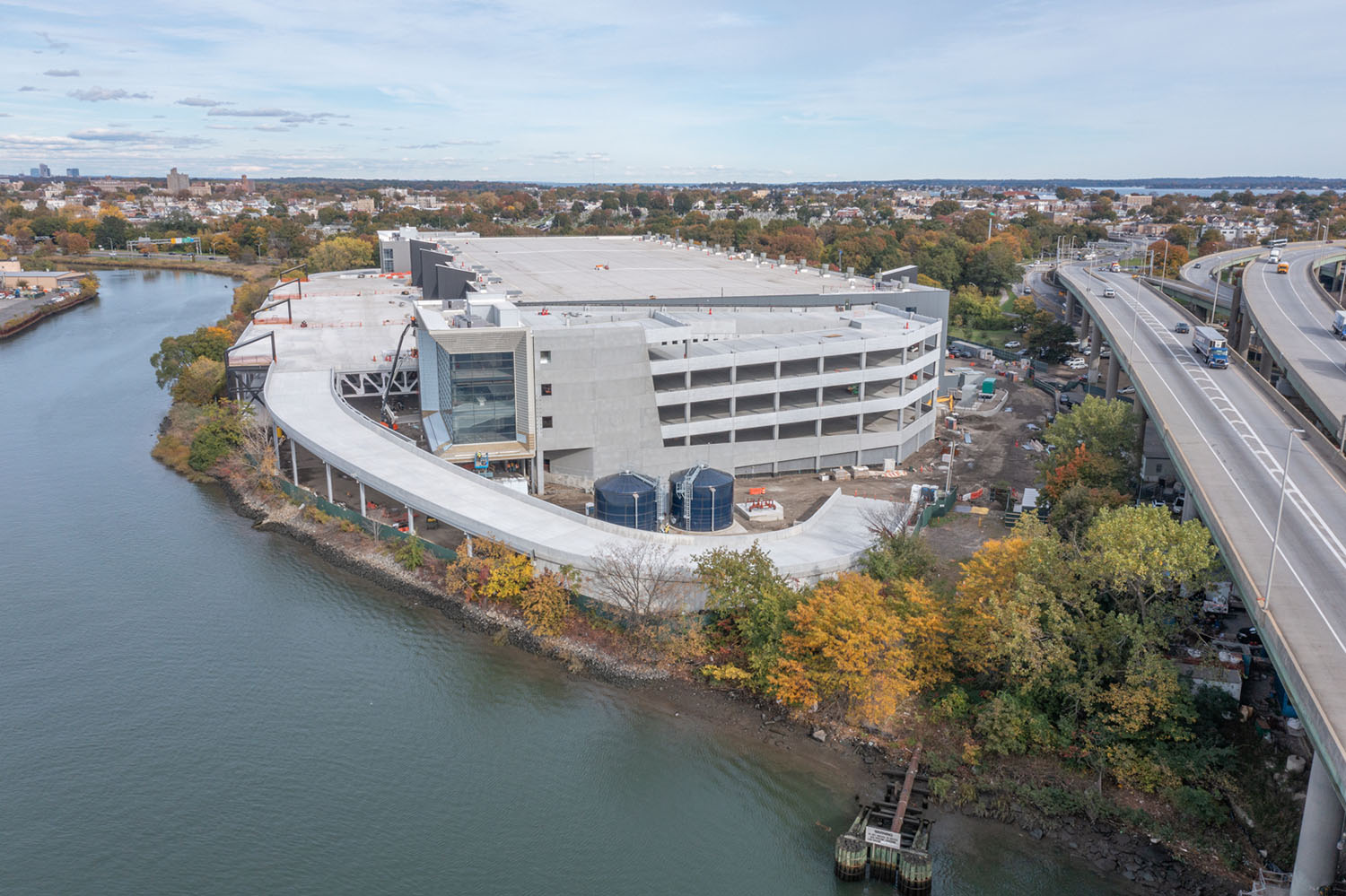
Bruckner Boulevard Parking Structure
The Bruckner Boulevard Parking Structure highlights stand-alone parking adjacent to a new state-of-the-art multi-story urban logistics facility in Bronx, NY. The two-level warehouse with 32-foot clear heights is flanked by a truck loading area and two precast parking structures. Adjacent parking structures were required to support the large warehouse. The "last mile" logistics center could not function efficiently without fleet storage and parking space.
Each parking structure is approximately 154,415 SF, with four elevated levels designed to accommodate parking. There are 664 interior parking spaces for cars and sprinter vans and 133 exterior parking spaces for trailers and box trucks in the new precast parking garages. The parking garages sandwiched between the warehouse and the exterior circular ramps will eventually support a solar panel array on the roof.
Advantages of Precast Concrete for Mixed-Use Parking
The numerous benefits of precast concrete make it an easy choice for owners, developers, designers, and contractors alike. By choosing precast concrete for stand-alone, mixed-use, or hybrid mixed-use structures, teams will realize these advantages:
Fast-Tracked Schedule - Offsite precast concrete fabrication is quicker than onsite construction. Production at the manufacturing facility is weather independent, reducing weather-related delays. Precast concrete requires smaller construction crews and can be installed in a limited construction footprint.
Improved Pre-Construction Planning - Precast concrete allows advanced planning that reduces design errors. Project teams can work closely in the pre-construction phase to streamline the design process and make value engineering decisions. Design assist contracts are becoming more common, enabling precasters to provide early input into value engineering, facilitating expedited schedules, and reducing precast costs.
Reliable Solution - Precast concrete is less susceptible to supply chain issues that cause fluctuating costs of competing building materials such as wood and steel. The unstable supply chain and labor shortages that afflict these other building materials are moving contractors to seek alternate designs to provide value and have driven the market to understand the advantages of precast.
Enhanced Quality - PCI Develops, maintains, and disseminates the Body of Knowledge to design, fabricate, and erect precast concrete structures and systems. Precast concrete panels constructed offsite in PCI-certified production facilities are of superior quality to those cast onsite. This is due to the uniform fabrication process possible at a separate casting facility and stringent quality control and quality assurance methods.
PCI Northeast has the resources to help you learn more!
Schedule A Design Office Presentation
Visit the PCI E-Learning Center
Discover Design Resources
Find a Precast Producer in NE and NY